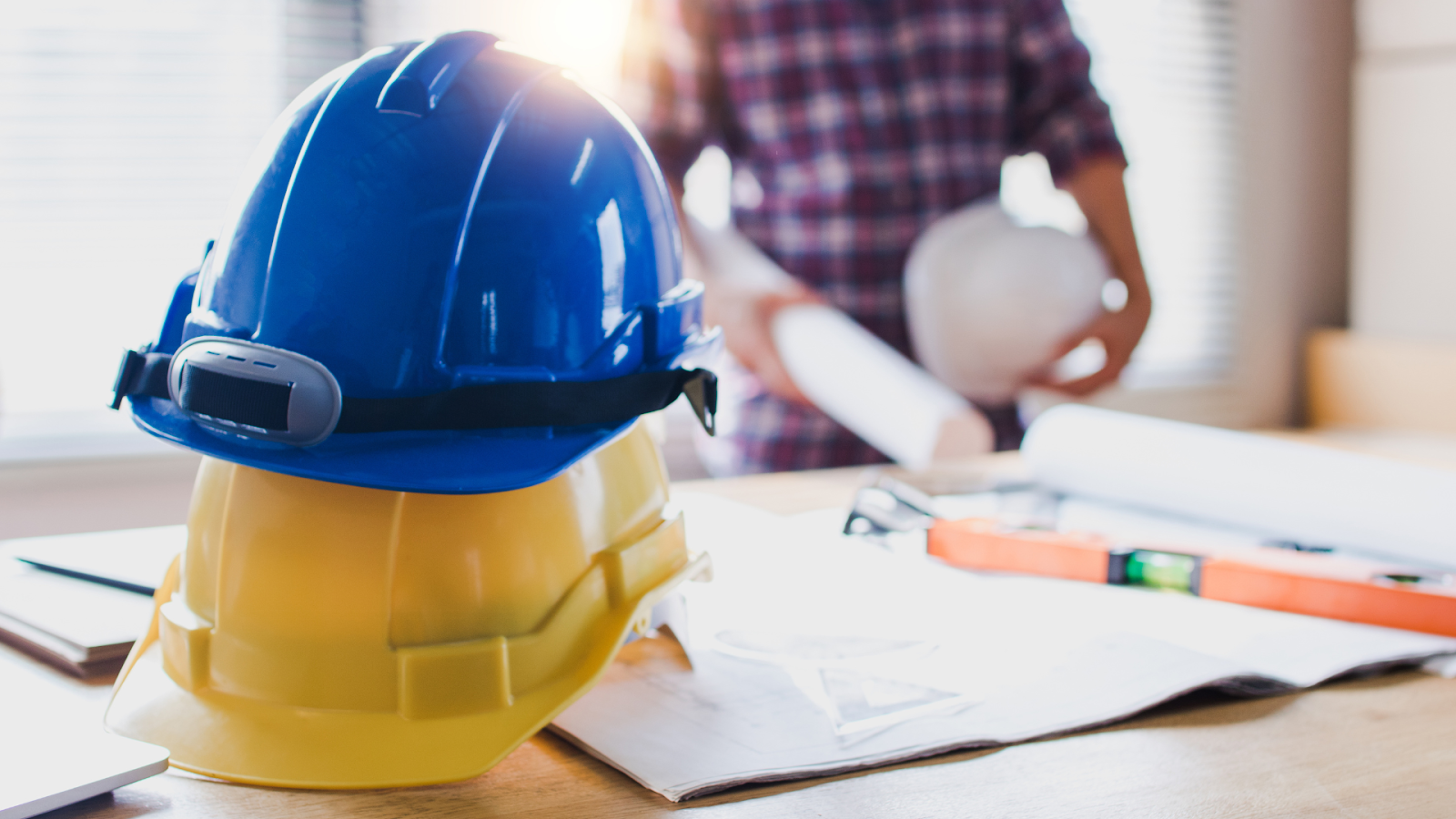
It’s no secret that accurate project estimation is crucial for profitability. One of the most effective methods for achieving accurate estimates every time is by applying first principles. This approach involves breaking down tasks into their base components and calculating costs based on the actual resources required.
Here’s a breakdown of the steps involved in using first principles to create an accurate estimate for your next construction project.
1. Resources
Understanding the resources needed for each task is the foundation of first principles estimation. Start by figuring out how many people are needed to complete a certain job. Take into account the skill level and labour costs here too.
2. Plant
Think about what equipment is required for a certain task. This includes machinery, tools, and any other equipment that will be used. Knowing the specific plant requirements helps in calculating the exact costs associated with the equipment.
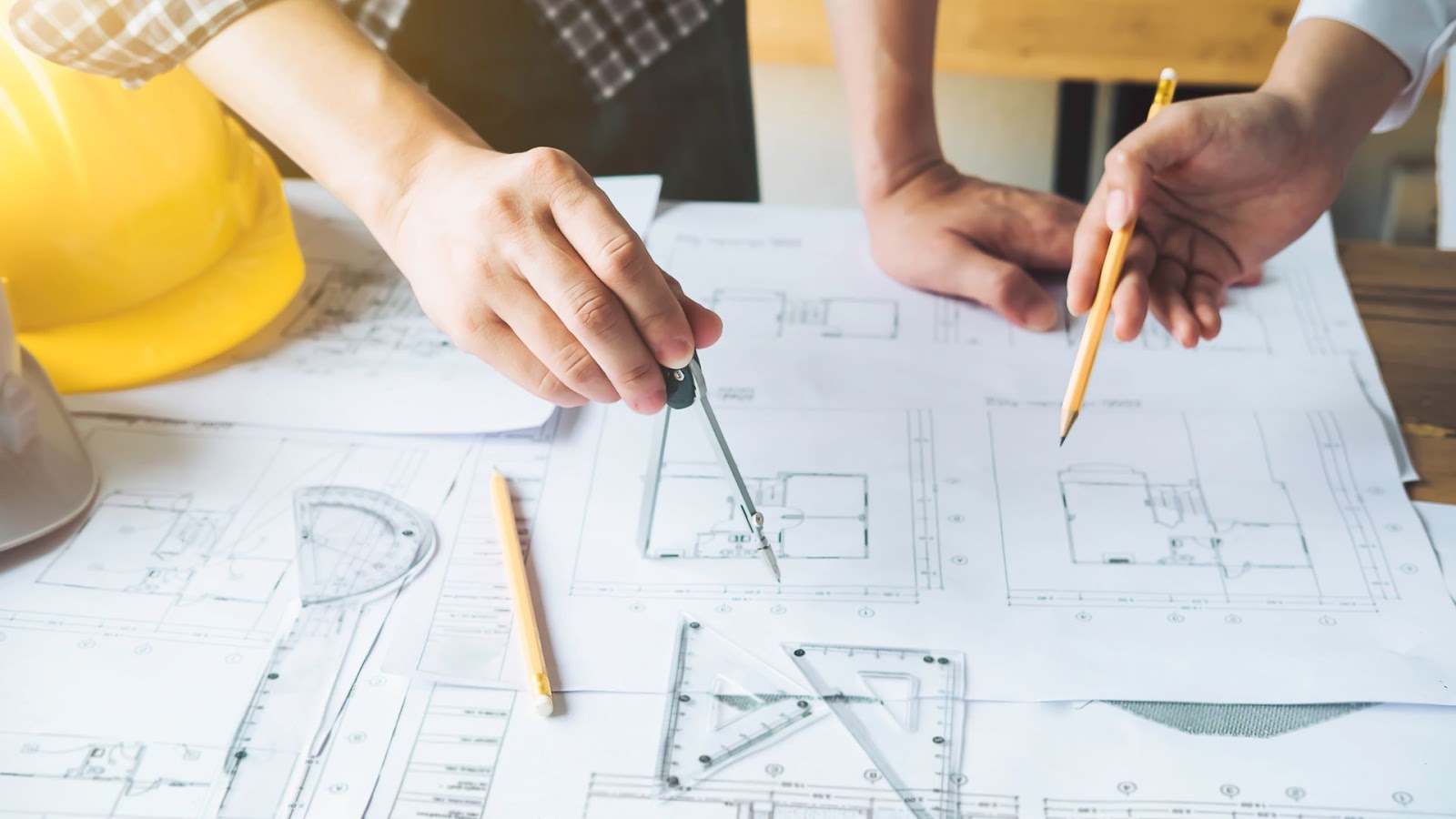
3. Subcontractors & Suppliers
Identify whether a subcontractor or supplier is needed within the project and for what stage. Factor in the costs of hiring these external resources to avoid underestimating the total project cost.
4. Materials
Accurate estimation of materials is critical. Think about the type and quantity of materials required for each job, like sand, stone, concrete, and cement. Detailed material estimates also make sure you have enough supplies without excessive overstock.
5. Overheads
Overheads are the indirect costs of running your business; think of the office, administrative costs and utilities. Someone has to pay for those too. Include those costs in your estimation to make sure they’re covered in the project budget.
6. Hiring Costs
Consider the hiring costs for both machines and labour. This includes rental fees for equipment and recruitment costs for labour. Accurate hiring cost estimates prevent unexpected expenses during the project.
7. Production
Estimate the cost and timeframe for completing the task. This includes the labour hours needed and production rates of your workforce and equipment.
8. Wastage
Account for wastage in your estimation. Determine the percentage of wastage for materials like concrete, stone, cement, and blocks. Including wastage in your calculations prevents material shortages and cost overruns.
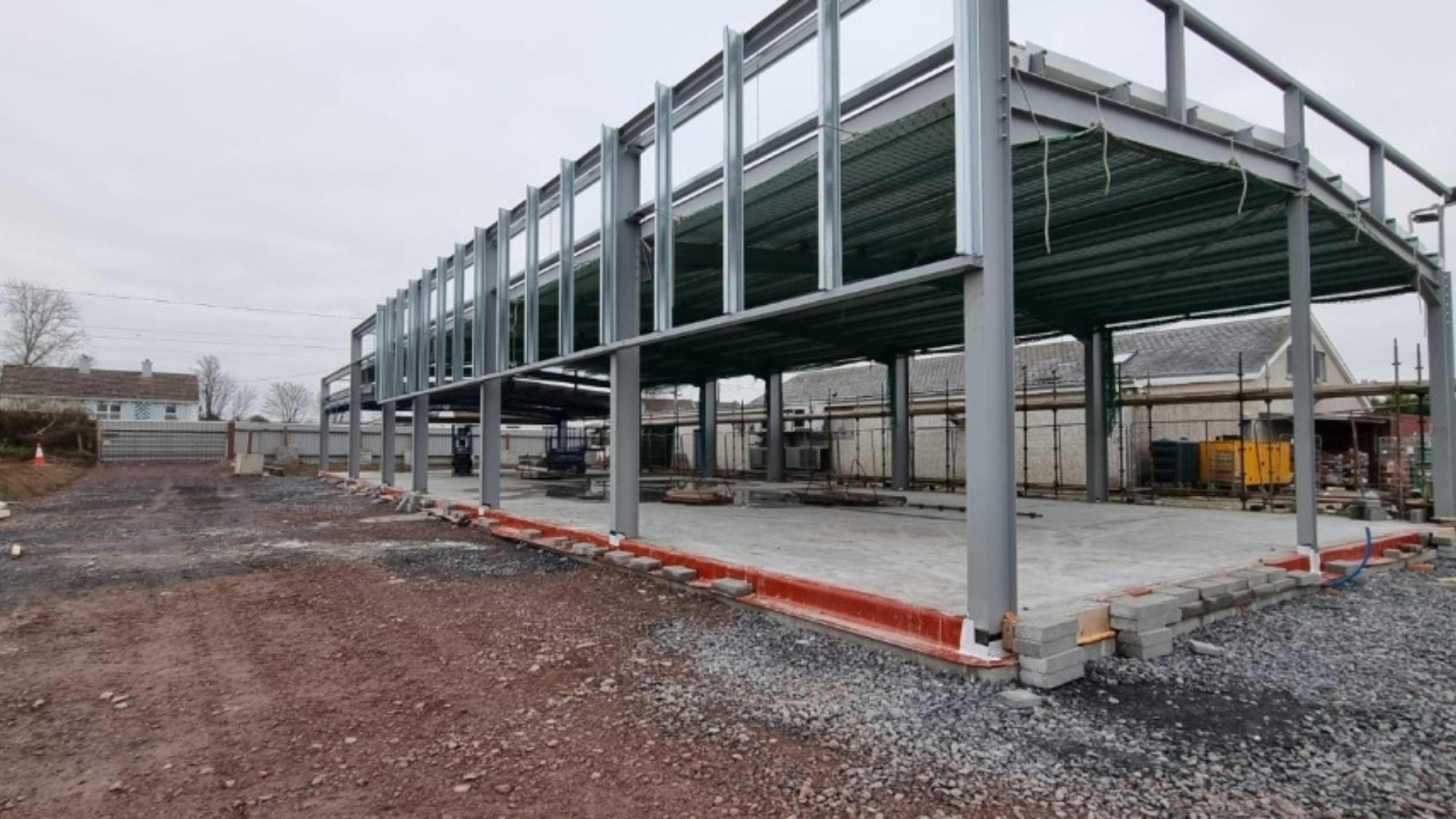
Building a Unit Rate
Combine all the above factors to create a unit rate for each task. Multiply the unit rate by the task’s quantity to get the total cost estimate.
Conclusion
When you use the first principles approach, you can develop more accurate rates. It’s a great way to build credibility and boost profitability in your business.
At Carroll Estimating, we use estimating software to ensure our rates are always accurate and up to date. Contact us today for your next tender and we’ll work alongside you from tender bid to final account and every step in between.